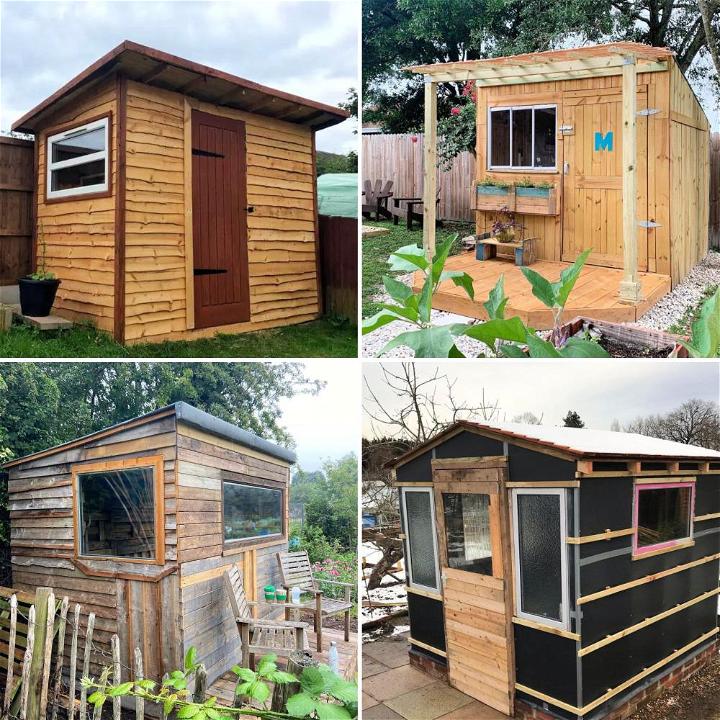
Free Pallet Shed Plans: Quick and Easy Steps to Build Your Shed
Hey there, fellow DIY enthusiasts! So you're looking to build a shed, huh? And you're hoping to do it on the cheap and without spending a fortune on lumber? Well, you've come to the right place! This guide will walk you through building a fantastic, functional shed using reclaimed pallets â" completely free (or nearly so!). Let's get started!Step 1: Gathering Your Materials â" The Pallet Hunt!
The best part about building a pallet shed? The materials are practically free! The most time-consuming part of this project is usually sourcing your pallets. Now, this isn't as easy as just walking down the street and grabbing them. Safety first! Make sure you're getting pallets that are clean, structurally sound, and haven't been treated with chemicals (like those marked "HT" for heat treatment, which are perfectly safe to use). Look for pallets from places like:
- Local businesses â" Many stores and businesses are happy to give away their used pallets once they're done with them. Just ask nicely!
- Construction sites â" Check with contractors in your area. They often have a surplus of pallets.
- Online classifieds â" Sites like Craigslist or Facebook Marketplace can be gold mines for free pallets.
- Recycling centers â" Some recycling centers might have pallets available.
Remember to check the condition carefully. You'll need a fair number of pallets, depending on the size of the shed you envision. Think about how many you need for the walls, the roof, and the floor. It's always better to have a few extras on hand, just in case!
Inspecting Your Pallets
Before you haul those pallets home, take a good look at them. Are the boards loose? Are there any broken or rotted pieces? Do any have protruding nails or staples that could be a hazard? You'll want to carefully remove any loose or damaged wood pieces and secure any loose nails, so you donât get injured during the building process. Consider using a hammer and nail puller to safely remove nails and replace damaged boards, this will ensure a safer and stronger final product.
Step 2: Designing Your Pallet Shed
Now for the fun part â" designing your shed! You can go as simple or as elaborate as you like. A basic shed can be as small as 4' x 6', while a more ambitious project could be 8' x 10' or even larger, depending on the number of pallets youâve acquired. Sketch out a simple design on paper, considering:
- Size: How much storage space do you need?
- Height: How tall do you want the shed to be?
- Door placement: Where will the door be located for easy access?
- Roof style: A simple gable roof is easiest for beginners.
You don't need fancy architectural drawings. A simple sketch is perfectly sufficient. Just make sure your measurements are accurate!
Step 3: Preparing the Pallets
Before you start building, you need to prep those pallets. This step is crucial for the structural integrity of your shed. Use a hammer and pry bar to remove any loose boards or nails, and replace any damaged pieces. Then give them a good cleaning â" you might want to use a wire brush to get rid of any dirt and debris.
Consider using a pressure washer, This will thoroughly clean the pallets and extend their lifespan. However, a good scrub with soap and water is also fine, but it may not be as effective in removing stubborn dirt.
Step 4: Assembling the Shed Frame
Now it's time to put it all together! Depending on your design, you might start with the floor, then build up the walls and finally the roof. Hereâs a basic outline:
- Floor: Lay down your pallets to create the base of your shed. Secure them together using screws and extra wood supports if needed. This will make the floor sturdy and prevent sinking into the ground
- Walls: Attach pallets vertically to create the walls, securing them firmly with screws and additional framing lumber if necessary, to create solid corner joints.
- Roof: For a simple gable roof, create triangular frames using extra lumber. Then attach the pallets to create the roof surface. Ensure the roof has a good slope for water drainage.
- Door: Cut a door opening in one of the walls and install a door using suitable lumber, or by repurposing extra pallets. Consider attaching sturdy hinges and a latch for security
You'll want to use galvanized screws and possibly additional framing lumber to strengthen the structure. It might be tempting to just nail things together, but screws provide a much stronger hold.
Step 5: Finishing Touches
Once the main structure is complete, it's time for the finishing touches! This could include adding:
- Exterior paint or sealant: This protects the wood from the elements and can give your shed a nice look.
- Interior shelving: Build simple shelves to maximize storage space. More pallets can be used for this purpose.
- A lock: Add a padlock or hasp for security to keep your items safe
- Tarpaulin: To provide extra weather protection. This ensures that your belongings are kept safe and dry in harsh weather conditions.
Commonly Asked Questions
Q: How long does it take to build a pallet shed?
A: The time it takes depends on the size and complexity of your design, your experience level, and the availability of tools. A simple shed could be built in a weekend, while a larger, more complex one could take several weekends.
Q: What tools do I need?
A: You'll need a hammer, pry bar, screwdriver, drill, measuring tape, saw (circular saw is best), safety glasses, work gloves, and possibly a level.
Q: How durable is a pallet shed?
A: The durability depends on the quality of the pallets you use and how well you construct the shed. With proper construction, a pallet shed can last for several years, especially with regular maintenance. Consider using treated lumber for parts that will be more exposed to the elements.
Q: Can I use any type of pallet?
A: No, always check for the heat-treated stamp ("HT") or use pallets you can confirm have not been treated with harmful chemicals. Avoid using pallets that are visibly damaged, rotted, or infested with insects.
Q: Do I need a permit to build a shed?
A: This depends on your local building codes. Check with your local authorities before you begin to ensure you are complying with all regulations.
There you have it! Building a pallet shed is a rewarding project that can save you money and provide valuable storage space. Remember to prioritize safety, plan carefully, and enjoy the process! Happy building!